Schweiß- und Schneidempfehlungen für Toolox®
TOOLOX®-QUALITÄTEN SIND ENGINEEING- UND WERKZEUGSTAHLSORTEN, DIE FÜR GÜNSTIGE SCHWEISSBARKEITS- UND SCHNEIDMERKMALE AUSGELEGT SIND.
Die folgenden Schweiß- und Schneidempfehlungen sollen das volle Potential Toolox-geschweißter Konstruktionen fördern. Wie für alle Arten von Engineering- und Werkzeugstahl nehmen die Anforderungen mit höherer Härte des Stahls zu. Dies bedeutet zum Beispiel, dass Toolox® 44 voll schweißbar ist, es aber nötig ist, sich genau an unsere Empfehlungen zu halten.
Alle konventionellen Schweiß- und Schneidverfahren können für diese Stahlsorten benutzt werden, und diese mit anderen schweißbaren Stahlsorten verschweißt werden.
Toolox® ist verfügbar als Bleche und Stangen. Alle Produkte aus diesen Stahlsorten werden in diesem Kontext angesprochen. Es wird auf unsere technischen Supportunterlagen (TechSupport) und WeldCalc™ Bezug genommen, die weitere Informationen zu bestimmten Punkten liefern. Jeder TechSupport behandelt weitere Informationen für bestimmte Bereiche, wie z.B. geeignete Zusatzwerkstoffe für Toolox-Schweißen.
Die Software WeldCalc erlaubt es Nutzern, die Schweißleistung in Bezug auf bestimmte Schweißsituationen weiter zu optimieren.
TechSupports findet sich unter www.ssab.com/download.
Eine Benutzerlizenz für WeldCalc kann man durch Registrierung auf der gleichen Homepage erhalten Sowohl TechSupports als auch WeldCalc sind kostenlos..
Schweißempfehlungen
SCHWEISSNAHTVORBEREITUNG
Die Schweißnahtvorbereitung kann mit allen konventionellen Methoden erfolgen, wie z.B. Thermoschneiden, Bearbeitungs- und Schleifstifte. Wenn Thermoschneiden eingesetzt wird, ist eine dünne Oxyd- oder Nitrid-Schicht vorhanden, die ca. bis zu 0,2 mm dick ist. Diese Schicht muss, normalerweise durch Schleifen, vor dem Schweißen entfernt werden. Empfehlungen für das Thermoschneiden werden unter einer separaten Überschrift spezifiziert..
Weiterhin sind Scheren und Stanzen für Blechdicken bis zu ca. 10 mm machbar.
Vor Aufbringen jeder Schweißlage ist es wesentlich, dass die Schweißvorbereitungsfläche von Verunreinigungen wie Feuchtigkeit, Fett, Rost und Öl gesäubert wird.
AUSWAHL VON SCHWEISSZUSATZWERKSTOFFE
Rostfrei, nichtlegierte und niedriglegierte Arten von Zusatzwerkstoffen sind für geschweißte Strukturen geeignet, die mäßigen Beanspruchungen unterliegen. Typischerweise haben die Nirosta-Ausführungen die besten Eigenschaften und sind in diesen Fällen im Allgemeinen vorzuziehen. Dies gilt besonders für das Schweißen von Toolox® 44.
Für Strukturen, wo die Schweißnähte hoher Beanspruchung ausgesetzt sind, sind niedriglegierte Zusatzwerkstoffe die beste Option.
Wesentliche Aspekte für die Auswahl von Zusatzwerkstoffen finden sich unten. Zusätzlich verfügt TechSupport über 60 Adressen als Beispiele für verschiedene Marken von Zusatzwerkstoffen und liefert ebenfalls detailliertere Informationen über die Auswahl von Zusatzwerkstoffen.
Rostfrei-Zusatzwerkstoffe
Alle Toolox®-Stahlsorten können mit Nirosta-Zusatzwerkstoffen vom Typ type AWS 307 oder AWS 309 geschweißt werden. Diese Klassifizierungsbezeichnungen gelten für Zusatzwerkstoffe zu allen konventionellen Schweißverfahren.
After welding, an even higher resistance is achieved to hydrogen cracks in the joint in relation to unalloyed and low-alloyed consumables. The microstructure of the all weld metal normally results in a high toughness where its’ yield strength is around 500 MPa. Due to the high resistance to hydrogen cracks no restriction applies of their hydrogen content.
Nach dem Schweißen wird sogar eine höhere Widerstandsfähigkeit gegen Andere wichtige Vorteile des Schweißens mit dieser Art von Zusatzwerkstoffen sind:
- Vorwärm/Zwischenlagentemperaturen, was eine Temperatur über +20 °C in der Schweißnaht sowie in der Umgebungsluft bedeutet, lassen sich für alle Produkte von Toolox® 33 vermeiden. Toolox® 44 muss mit einer Vorwärmung nach der untenstehenden Tabelle geschweißt werden.
- Verschweißen mit anderen Stahlarten als nichtlegierten und niedriglegierten Stahlarten möglich, z.B.:
- Rostfrei
- Manganstahl (Hadfield Stahl)
In diesem Fall gelten Schweißbedingungen, die sowohl für Toolox® als auch für die anderen Arten zu schweißenden Stahls geeignet sind.
Die erste Präferenz sind Zusatzwerkstoffe nach AWS 307. Der Hauptunterschied zwischen ihnen besteht darin, dass bei Verwendung von Zusatzwerkstoffen des Typs AWS-307 die Heißrissbeständigkeit im Vergleich zum Typ AWS-309 etwas höher ist.
Nachteile mit den angegebenen Nirosta-Zusatzwerkstoffen sind, dass:
- Das Gasschneiden kann an Schweißnähten nicht durchgeführt werden. Jedoch sind sowohl Plasma- als auch Laserschneiden in diesem Fall durchführbar. Wenn in dieser Situation Gasschneiden verlangt wird, sind nichtlegierte oder niedriglegierte Zusatzwerkstoffe zu verwenden. Das Schweißgut, das von den zuletzt erwähnten Zusatzwerkstoffen erzeugt wird, kann mit allen Thermoschneidmethoden geschnitten werden.
- Die Zusatzwerkstoffe sind, im Vergleich zu nichtlegierten und niedriglegierten Ausführungen, teurer.
Nichtlegierte und niedriglegierte Zusatzwerkstoffe
Nichtlegierte und niedriglegierte Zusatzwerkstoffe sollten die spezifizierten Festigkeitskriterien erfüllen, und ihr Wasserstoffanteil sollte ausreichend niedrig sein.
Geeignete Zusatzwerkstoffe sind in einer großen Festigkeitspalette verfügbar. Für die meisten Anwendungen bedeutet dies Ausführungen mit einer Streckgrenze im geschweißten Metall bis zu ca. 930 MPa.
Es ist oft günstig, einen Zusatzwerkstoff mit einer niedrigen Festigkeit und einer Streckgrenze von ca. 500 MPa einzusetzen. Die Gründe dafür sind, dass:
- Die Widerstandsfähigkeit gegen Wasserstoffrisse zunimmt
- Eine höhere Zähigkeit im Schweißgut oft von einem Zusatzwerkstoff mit niedrigerer Festigkeit befördert wird
Niedriglegierte Zusatzwerkstoffe mit einer Streckgrenze bis zu ca. 930 MPa sind möglich, und sie können zum Schweißen von Toolox verwendet werden. Diese Zusatzwerkstoffe können im Schweißgut eine vorteilhafte Zähigkeit erreichen, die die erforderliche Zähigkeit der Toolox-Qualitäten erfüllen kann.
Mit der höchstmöglichen Härte im Schweißgut ist es möglich, Toolox mit besonders für das Schweißen von Engineering- und Werkzeugstahlsorten ausgelegten Zusatzwerkstoffen zu schweißen. Diese Zusatzwerkstoffe können im Schweißgut eine sehr hohe Härte erreichen. Jedoch wird die vorteilhafte Zähigkeit normalerweise für diese Produkte nicht hervorgehoben. Kontaktieren Sie SSAB für weitere Informationen zur Auswahl dieser Art von Zusatzwerkstoffen.
Die Wasserstoffkriterien sind für alle nichtlegierten und niedriglegierten Zusatzwerkstoffe auf ein Maximum von 5 ml Wasserstoff(100 g Schweissgut festgelegt, um Wasserstoffrisse in der Schweißnaht zu vermeiden. Es gibt Zusatzwerkstoffe für alle Schweißverfahren, die diese Anforderung erfüllen können.
Alle Volldrähte für MAG, TIG und Plasmaschweißen können die Wasserstoffkriterien erfüllen.
Zusatzwerkstoffe, die ein Flussmittel oder eine Beschichtung benutzen, sind eine zusätzliche Quelle für die Feuchtigkeitsaufnahme. Die Zusatzwerkstoffkategorien, die ausreichend niedrige Wasserstoffwerte erreichen können, werden in der untenstehenden Tabelle erwähnt. Diese Information dient als allgemeine Richtschnur für die Auswahl von Zusatzwerkstoffen. Das Wasserstoffpotential für einen bestimmten Zusatzwerkstoff betreffende Informationen können von seinem Lieferanten geleifert werden.
Zusatzwerkstoffe, die das Potential haben einen ausreichend niedrigen Wasserstoffanteil zum Schweißen von
Toolox-Qualitäten zu erreichen. |
Nichtlkegierte und niedriglegierte Zusatzwerkstoffe |
Arten von Zusatzwerkstoffen |
Volldrähte (MAG- und TIG-Schweißen) |
Alle Arten |
Drähte mit Flussmittelkern (MAG)) |
Basis- und Rutilvariantens |
Drähte mit Metallkern (MAG) |
Bestimmte Ausführungen. Siehe das Datenblatt für die Zusatzwerkstoffe |
Zusatzwerkstoffe für MMA-Schweißen |
Basisvarianten |
Zusatzwerkstoffe für SAW |
Basis-Flussmittel/Fülldrahtkombinationen |
Schweißzusatzwerkstoffe, EN-Klasse |
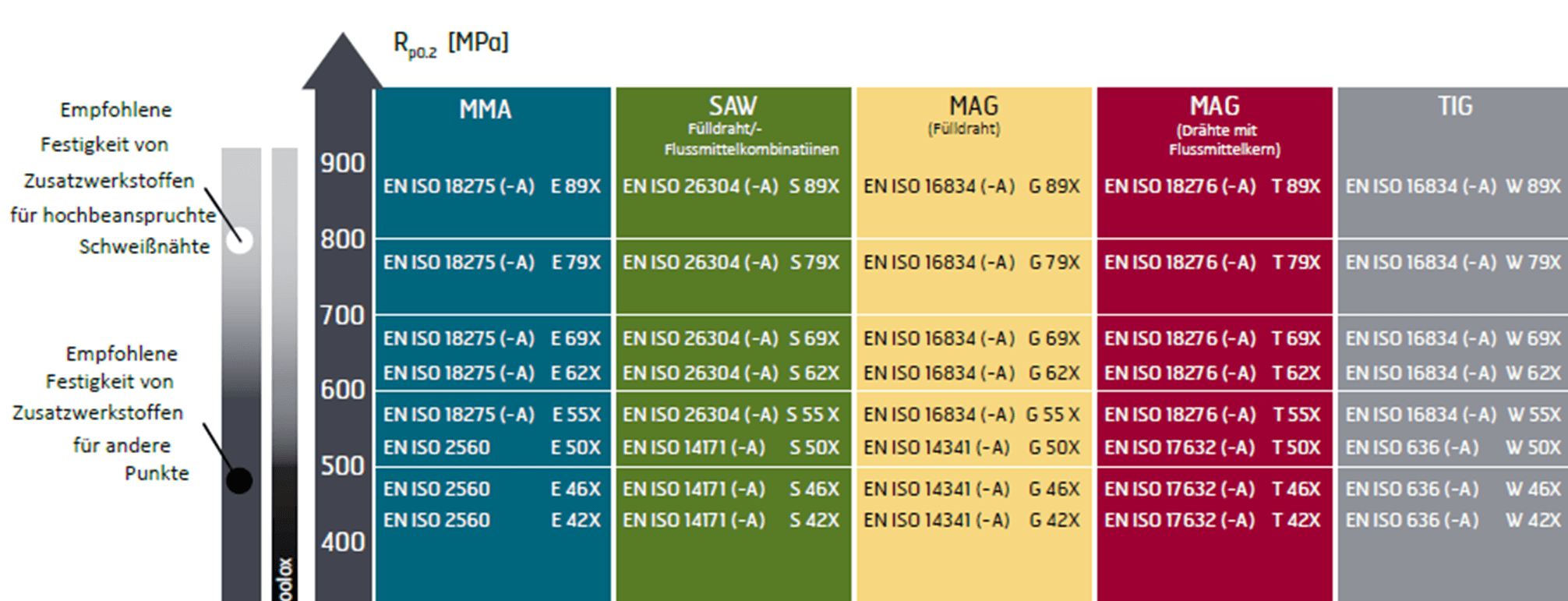 |
Schweißzusatzwerkstoffe, AWS class |
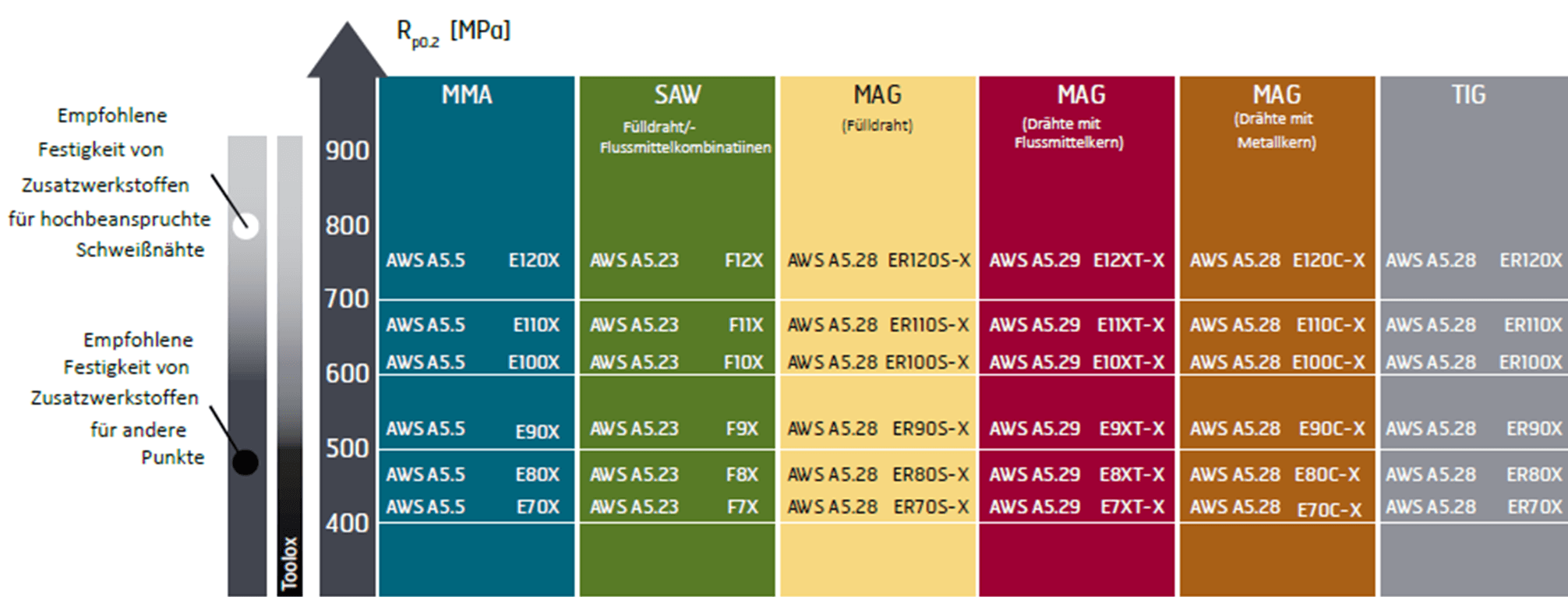 |
SCHUTZGAS
Für Schweißverfahren, die Schutzgas verwenden, hängen Auswahl und Gemisch der Gase von der Schweißsituation ab. Gemische von Argon (Ar) und Kohlendioxyd (CO2) sind die weitest verbreiteten.
Bei allen schutzgasbasierten Schweißverfahren hängt der Schutzgasfluss von der Schweißsituation ab. Ein zu niedriger Gasfluss kann zu einem unzureichenden Gasschutz der Schmelze führen. Ein zu starker Gasfluss kann turbulent werden und so den Gasschutz beeinträchtigen. Eine allgemeine Richtschnur ist die, dass der in ml/min gemessene Schutzgasfluss auf den gleichen Wert eingestellt wird wie der in mm gemessene Innendurchmesser des Schweißbrenners.
Schweißzusatzwerkstoffe, AWS class |
- Facilitates striking of the arc
- Reduced spatter
- Low amount of oxides
|
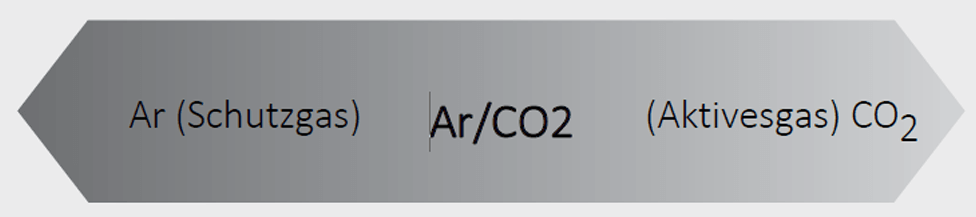 |
- Stable arc
- Low porosity
- More weld spatter/clogging of the welding nozzle
- High penetration of the weld metal
|
Beispiele für Schutzgasgemische |
Schweißverfahren |
Lichtbogenart |
Position |
Schutzgas |
MAG, Volldraht |
Kurzer Lichtbogen |
Alle Positionen |
18-25% CO2 rest. Ar |
MAG, Fülldraht |
Kurzer Lichtbogen |
Alle Positionen |
18-25% CO2 rest. Ar |
MAG, Volldraht |
Sprühlichtbogen |
Horizontal (PA, PB, PC) |
15-20% CO2 rest. Ar |
MAG, FCAW |
Sprühlichtbogen |
Alle Positionen |
15-20% CO2 rest. Ar |
MAG, MCAW |
Sprühlichtbogen |
Horizontal (PA, PB, PC) |
15-20% CO2 rest. Ar |
Roboter und automatisch MAG |
Sprühlichtbogen |
Horizontal (PA, PB, PC) |
8-18% CO2 rest. Ar |
TIG |
Sprühlichtbogen |
Alle Positionen |
100% Ar |
WÄRMEEINTRAG
Der Wärmeeintrag durch eine Schweißung beschreibt die an die Schweißnaht abgegebene Energie/Länge. Der Wert
des Wärmeeintrags berührt die mechanischen Eigenschaften der Schweißnaht. Der Wärmeeintrag hängt ab vom angewandten Schweißverfahren sowie vom Strom- und Spannungswert und der Verfahrgeschwindigkeit des Schweißverfahrens.
Beim Schweißen geht Energie im Lichtbogen verloren. Der thermische Wirkungsgradfaktor (k) drückt den Teil des Wärmeeintrags aus, der an die Schweißnaht abgegeben wird. Verschiedene Schweißverfahren haben unterschiedliche thermische Wirkungsgradfaktoren entsprechend dem Untenstehenden. Siehe unten für angenäherte Werte von k und wie der Wärmeeintrag berechnet wird.
Kontaktieren Sie für besondere Anforderungen in Bezug auf bestimmte mechanische Eigenschaften in den Toolox-Schweißnähten SSAB für weitere Unterstützung bezüglich der Wärmeeintragsauswahl.
Der Wärmeeintrag kann mit der untenstehenden Formel
berechnet werden |
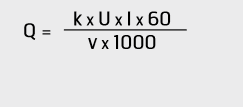 |
Q = Wärmeeintrag [kJ/mm]
U = Spannung [V]
I = Strom [A]
v = Wärmeeintrag [mm/min]
k = Thermischer Wirkungsgrad
[dimensionslos] |
Schweißverfahren |
Thermischer Wirkungsgrad
(dimensionslos)] |
MMA |
0.8 |
MAG, all types |
0.8 |
SAW |
1.0 |
TIG |
0.6 |
Allgemeine Auswirkugnen des Wärmeeintrags auf eine Schweißnaht |
- Bessere Zähigkeit
- Erhöhte Festigkeit
- Reduzierte Verformung
- Niedrigere
Restbeanspruchungen
- Engerer HAZ
|
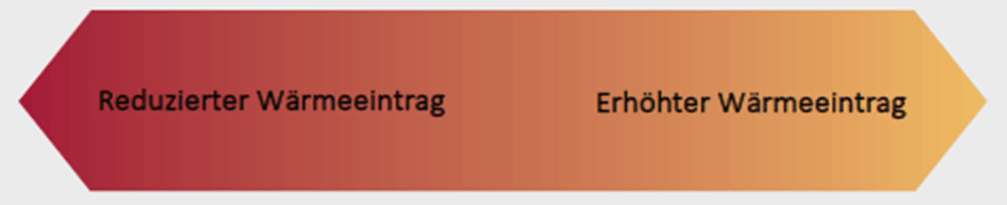 |
- Eine höhere
Produktivität für die konventionellen
Schweißverfahren
|
Vermeidung von Wasserstoffrissen
Beim Schweißen können sich in verschiedenen Stahlsorten Wasserstoffrisse bilden, aber sie treten deutlicher in allen hochfesten Stahlsorten, einschließlich Toolox, zu Tage. Das Risiko dieser Art von Rissen wird durch Befolgung der Empfehlungen in dieser Broschüre minimiert.
Vom Stahlgesichtspunkt aus steht der Widerstand in Beziehung zur chemischen Zusammensetzung des Stahls. Generell gilt, je geringer der Wert der Legierungen, umso höher der Widerstand gegen Wasserstoffrisse. Erhöhte Legierungswerte werden in der Regel hinzugefügt, um folgendes zu erreichen:
- Erhöhte Härte und Festigkeit des Stahls
- Einheitliche mechanische Eigenschaften über dieganze Dicke des Blechs
Kohlenstoffäquivalent wird gewöhnlich als CEV oder CET in Übereinstimmung mit der untenstehenden Gleichung ausgedrückt. Je niedriger das Kohlenstoffäquivalent umso höher die Wasserstoffrissbeständigkeit im Stahl.
Typische und max. Werte für Kohlenstoffäquivalent werden in unserem Produktdatenblatt für jede Toolox-Qualität angegeben, und sie hängen auch von Blechdicke/Durchmesser der Stahlsorte ab. Es besteht jedoch keine Notwendigkeit, das Kohlenstoffäquivalent zu berechnen, um unsere in dieser Broschüre vorgestellten Schweißempfehlungen zu befolgen.
In den folgenden Tabellen werden die Kohlenstoffäquivalente für die Toolox-Qualitäten mit einigen Produkten verglichen, die gewöhnlich für Werkzeug und bearbeitete Komponenten benutzt werden.
WasserstoffrissenToolox®-Stahl hat typischerweise erheblich höhere Kohlenstoffäquivalentwerte als andere Werkzeug- und Engineeringstahlsorten mit vergleichbaren Härtewerten. Als Folge ist die Gesamtschiweißbarkeit von Toolox in Bezug auf andere Werkzeug/Maschinenstahlsorten erheblich höher.
Kohlenstoffäquivalente für Toolox® 33 im Verhältnis zu anderen Werkzeug/Maschinensthlarten mit ähnlichen HärtewertenKohlenstoffäquivalente |
Stahl |
CET [%], typische Werte |
CEV [%], typische Werte |
Toolox® 33 |
0.38–0.42 |
0.63–0.71 |
AISI: 4140 / EN: 42CrMo4 |
1.13 |
1.27 |
AISI: 4340 / EN: 34CrNiMo6 |
0.58 |
0.85 |
AISI: 1045 / EN: C45 |
0.52 |
0.57 |
HärtewertenKohlenstoffäquivalente für Toolox® 44 im Verhältnis zu anderen Werkzeug/Maschinensthlarten mit ähnlichen Härtewerten |
Stahl |
CET [%],typische Werte |
CEV [%], typische Werte |
Toolox® 44 |
0.57 |
0.96 |
AISI: H13 / EN: 1.2344 |
0.83 |
1.89 |
Zwei Regeln für die Vermeidung von WasserstoffrissenToolox |
1) Minimierung des Wasserstoffanteils in der und um die Schweißnaht herum:
- Wenn erforderlich, die richtige Vorwärme- und Zwischenlagentemperatur der Schweißnaht anwenden
- Schweißzusatzwerkstoffe mit ausreichend niedrigem Wasserstoffanteil in Übereinstimmung mit den Empfehlungen von SSAB einsetzen
- Verunreinigungen vom Schweißbereich fernhalten.
|
2) Den Beanspruchungswert in der und um die Schweißnaht herauf einem ausreichend niedrigen Wert halten:
- Die Schweißnaht mit einer kleinen min. Spaltweite vorbereiten
- Die Schweißfolgen so anordnen, dass restliche Beanspruchungen minimiert werden
- Keine Zusatzwerkstoffe mit höheren Festigkeitswerten als notwendig benutzen.
|
Schweißnahtgeometrie
Wenn Toolox durch den Mittenquerschnitt der Blechdicke geschweißt wird, werden für Blechdicken/Durchmesser über 25 mm asymmetrische Schweißnähte empfohlen. Dies liefert eine zusätzliche Wasserstoffrissbeständigkeit für die ersten Wurzellagen. Die Gründe dafür sind, dass:
- Der Mittelteil des Bleches n einem gewissen Umfang chemische Elemente enthalten kann, die die Bildung dieser Art Risse unterstützen können. Je größer die Blech/Stangendicke umso ausgeprägter wird dieser Punkt auftreten.
- Die Wurzellagen empfindlicher gegen Wasserstoffriss sind. Schweißnähte mit einer Blechdicke/Durchmesser bis zu 25 mm können entweder symmetrisch oder asymmetrisch sein.
Große Wurzelspalten in Schweißnähten halten höhere Beanspruchungskonzentrationen aus, was den Widerstand gegen Wasserstoffrisse reduziert. SSAB empfiehlt, die Größe des Wurzelspalts auf max. 3 mm einzustellen, um Beanspruchungskonzentrationen zu reduzieren.
Schweißfolge
Start- und Stoppfolgen von Schweißungen werden vorzugsweise 50 – 100 mm von Ecken einer Schweißnaht entfernt vorgesehen, um zu große Restbeanspruchungen in der Schweißnaht zu vermeiden.
Schweißnaht bei der Plattendicke über 25mm |
Asymmertrische Schweißnaht; der Mittelpunkt der Naht wird vorzugsweise ca. 5 mm vom Mittelpunkt der Blechdicke entfernt gewählt
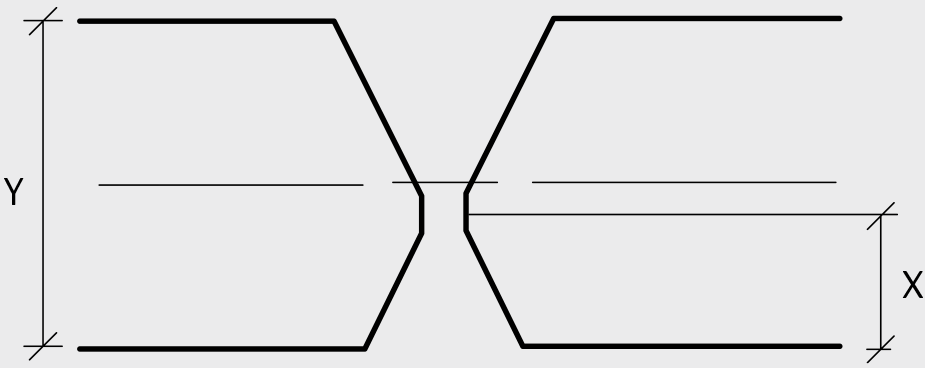 |
Y: Blechdicke
|
X: (Blechdicke/2)-5 mm
|
Maximum Deposit 3 mm |
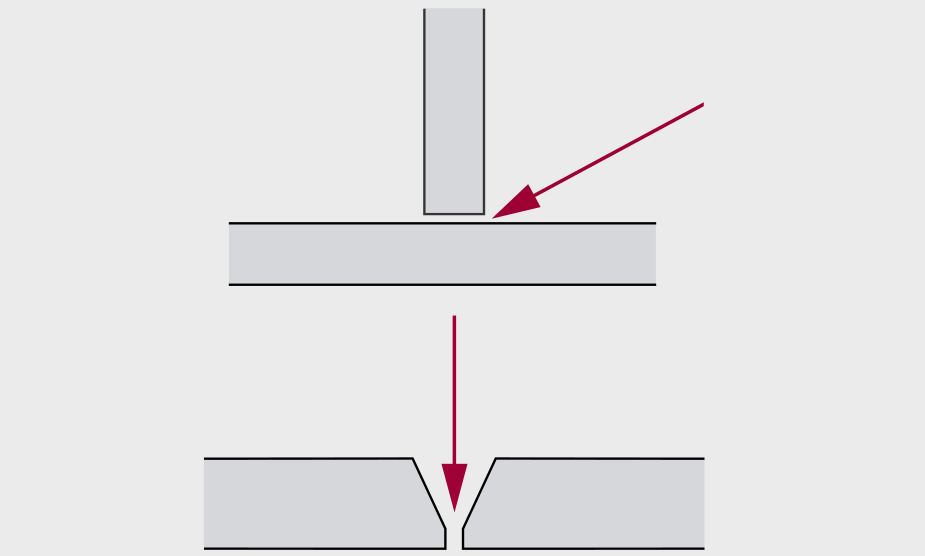 |
Schweißfolgen |
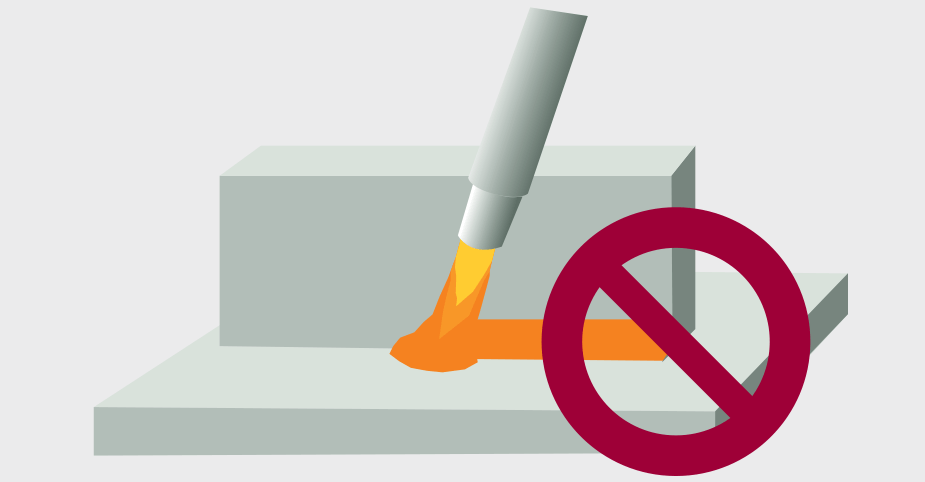 |
Vorwärmempfehlungen
Eine Vorwärmung ist in vielen Fällen notwendig, um das Risiko von Wasserstoffrissen zu minimieren. Vorwärmen erleichtert einen schnellen Austritt des Wasserstoffs aus der Schweißnaht. Es ist von wesentlicher Bedeutung, dass die erforderlichen Vorwärmtemperaturen eingehalten werden und dass das Verfahren sorgfältig durchgeführt wird. Es ist essentiell, dass die Vorwärmung, wenn erforderlich, auch für Heftschweißungen durchgeführt wird. Jede Heftschweißung soll vorzugsweise mindestens 50 mm lang sein. Kontaktieren Sie SSAB für weitere Informationen, wenn Heftschweißen unter 50 mm erforderlich ist.
Die Notwendigkeit der Vorwärmung ist unterschiedlich zwischen Schweißen mit nichtlegiertem und niedriglegiertem Zusatzwerkstoffen und Schweißen mit Nirosta-Zusatzwerkstoffen.
- Wenn eine Verbindung aus Blech unterschiedlicher(m) Blechdicke/Stangendurchmesser der gleichen Toolox-Qualität besteht, bestimmt die stärkste Blechdicke/der stärkste Durchmesser die erforderliche min. Vorwärm- und Zwischenlagentemperatur.
- Wenn eine Toolox-Qualität mit einem Stahl anderer Qualität verschweißt wird, bestimmt das Blech/die Stange, die die höchste min. Vorwärmtemperatur verlangt, die min. Vorwärm- und Zwischenlagentemperatur..
- Wenn in der untenstehenden Tabelle keine Vorwärmung angegeben ist. Ist für Wärmeeinträge im Bereich von 1,0-1,6 kJ/mm keine Vorwärmung erforderlich.
Die min. Vorwärmtemperatur für Schweißen mit allen empfohlenen Zusatzwerkstoffen wird, verglichen mit dem obigen Diagramm, für alle folgenden Situationen um 25°C erhöht:.
- Für Wärmeeinträge im Bereich von 1.0–1.6 kJ/mm: Wenn min. Vorwärmtemperaturen über Raumtemperatur in der obigen Tabelle angegeben sind.
- Für Schweißnähte mit sehr hohen Einschränkungen.
- Für Temperaturen unter +5°C in der Umgebungsluft und/ oder in den Blechen/Stangen..
- Wenn Schweißen in einem sehr feuchten Klima durchgeführt wird..
Min. Vorwärmtemperaturen für Schweißen mit Wärmeeinträgen < 1.0 kJ/mm lassen sich z.B. mit der von SSAB entwickelten Software oder durch Anwendung einer relevanten Norm für diese Maßnahme berechnen.
Die max. Vorwärmtemperaturen werden für alle Schweißverfahren auf +580°C festgesetzt und gelten für alle Toolox-Produkte. Sie soll günstige mechanische Eigenschaften in der Schweißnaht erreichen.
Einzelblechdicke |
Die Temperatur des dicksten Blechs an der Schweißnaht messen. Es sollte eine Wartezeit von mindestens 2 min/25 mm Dicke vor Messen der Vorwärmtemperatur eingehalten werden. Die min. Vorwärmtemperatur sollte für eine Fläche von 75+75 mm rundherum um die vorgesehene Schweißbaht ermittelt werden. |
Die erforderlichen Vorwärm- und Zwischenlagentemperaturen lassen sich auf verschiedene Art und Weise erreichen. Heizöfen oder elektrische Vorwärmelemente rundherum um die vorbereitete Schweißnaht sind oft am besten, da sie eine einheitliche Erwärmung der gleichen Fläche liefern. Die Temperatur sollte z.B. durch ein Pyrometer oder ein Kontaktthermometer kontrolliert werden.
Unlegierte Und niedriglegierte Zusatzwerkstoffe – Min. Vorwärme- und Zwischenlagentemperaturen [°C] |
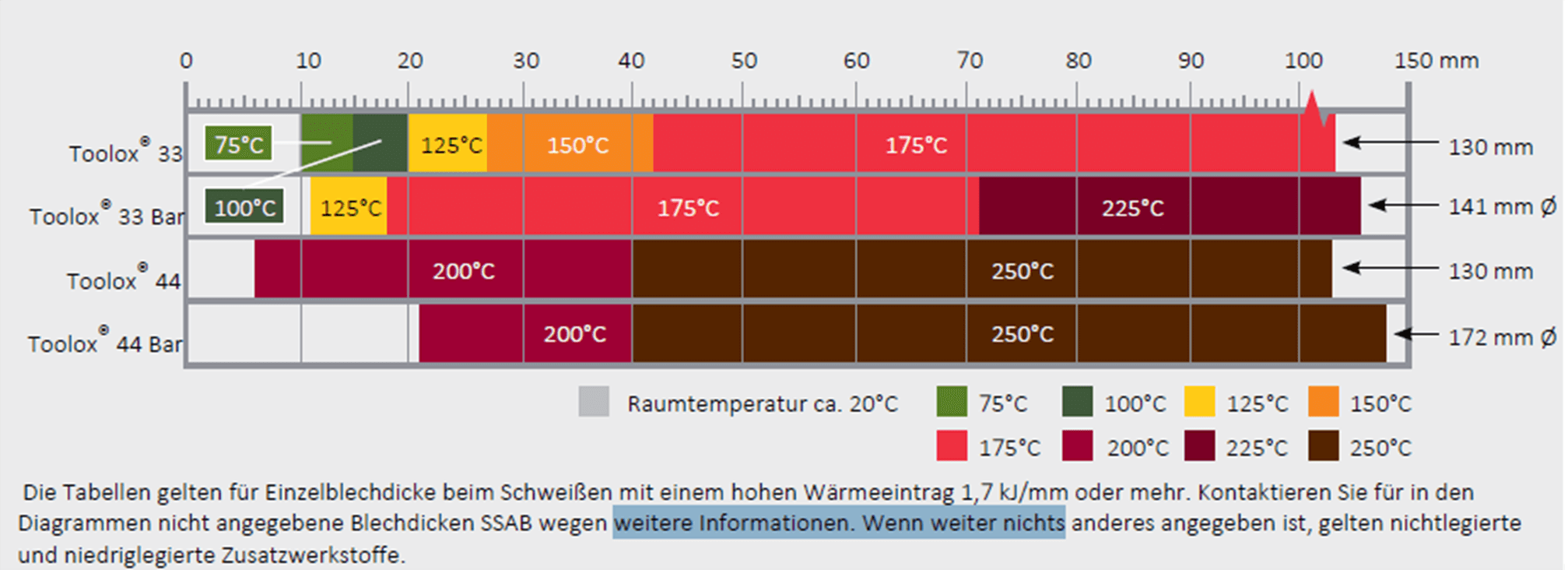 |
Stainless consumables – minimum preheat and interpass temperatures [°C] |
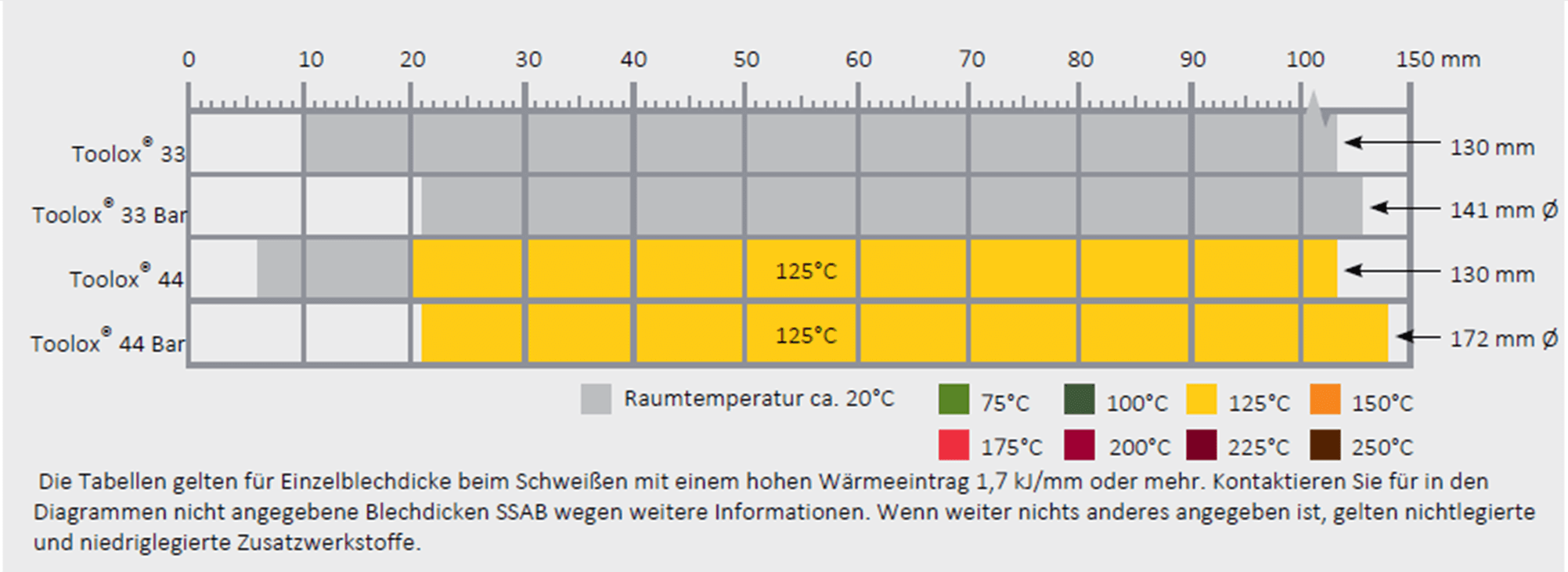 |
SCHWEISSEN AUF GRUNDIERTEN BLECHEN
Die Toolox®-Stahlqualitäten können mit einem Primer als Mittel gegen Korrosion geliefert werden. Das Schweißen kann wegen seines niedrigen Zinkanteils direkt auf dem Primer durchgeführt werden. Der Primer kann in dem Bereich rundherum um die Schweißnaht leicht abgebürstet oder abgeschliffen werden. Die Entfernung des Primer vor dem Schweißen kann die Porosität im Schweißgut minimieren und das Schweißen in anderen Positionen als der horizontalen erleichtern. Wenn der Primer nicht entfernt wird, wird sich die Porosität leicht erhöhen. Das MAG-Verfahren mit Basisausführungen von Flussmittelkerndrähten und das MMA-Schweißverfahren bieten die niedrigste Porosität. Wie bei allen Schweißarbeiten muss eine gute Lüftung aufrechterhalten werden, um schädliche Auswirkungen auf den Schweißer und seine Umgebung zu vermeiden. Weitere Informationen hierzu finden sich in TechSupport Nr. 25.
Stahl |
Haltetemperatur [°C] |
Haltetemperatur [°C/h] |
Haltezeit [min/mm*] |
Haltezeit [h] |
Toolox® 33 |
550–590 |
100 |
2 |
1–6 |
Toolox® 44 |
540–580 |
100 |
2 |
1–6 |
*Blechdicke oder min. Durchmesser
WELDING ON PRIMED PLATES
Die Toolox®-Stahlqualitäten können mit einem Primer als Mittel gegen Korrosion geliefert werden. Das Schweißen kann wegen seines niedrigen Zinkanteils direkt auf dem Primer durchgeführt werden. Der Primer kann in dem Bereich rundherum um die Schweißnaht leicht abgebürstet oder abgeschliffen werden. Die Entfernung des Primer vor dem Schweißen kann die Porosität im Schweißgut minimieren und das Schweißen in anderen Positionen als der horizontalen erleichtern. Wenn der Primer nicht entfernt wird, wird sich die Porosität leicht erhöhen. Das MAG-Verfahren mit Basisausführungen von Flussmittelkerndrähten und das MMA-Schweißverfahren bieten die niedrigste Porosität. Wie bei allen Schweißarbeiten muss eine gute Lüftung aufrechterhalten werden, um schädliche Auswirkungen auf den Schweißer und seine Umgebung zu vermeiden. Weitere Informationen hierzu finden sich in TechSupport Nr. 25.
WERKSTOFFGRUPPIERUNGEN NACH DER EUROPÄISCHEN NORM EN 15608
Bei Durchführung von Qualifikationen von Schweißverfahren gehören die Stahlgruppierungen aller Toolox-Qualitäten, einschließlich ihres vollen Dickenbereiche, zur Werkstoffgruppe 3.2..
VERSCHWEISSEN VON TOOLOX® MIT ANDEREN STAHLARTEN
Wenn eine Toolox-Qualität mit anderen Stahlarten verschweißt wird, sind Schweißbedingungen anzuwenden, die zu jedem in der Schweißnaht verwendeten Stahl passen..
Thermoschneidempfehlungen
Der niedrige Legierungsanteil der Toolox-Qualitäten trägt zu ihren vorteilhaften Eigenschaften hinsichtlich des Thermoschneidens bei, wie zum Beispiel ihre Beständigkeit gegen Wasserstoffrisse durch das Schneiden. In dieser Hinsicht ist der Einfluss von Legierungen auf den Stahl in der Schneid- und Schweißtechnik ähnlich. Als ein Ergebnis führen die günstigen Kohlenstoffäquivalentwerte von Toolox beim Schneiden zu einem erhöhten Widerstand gegen Wasserstoffrisse. Die Definition von Kohlenstoffäquivalent wird in den Schweißempfehlungen unter der Überschrift Vermeidung von Wasserstoffrissen beschrieben.
Die inhärente hohe Zähigkeit der Toolox-Qualitäten reduziert das Risiko von während des Thermoschneidens erzeugter Mängel weiter. In der industriellen Praxis macht es dies möglich. Nichtquadratische Formen weitaus produktiver als durch die typischerweise extensive maschinelle Bearbeitung anderer Arten von Werkzeug- und Maschinenstahls zu produzieren.
Alle Verfahren des Thermoschneidens können für alle Toolox-Produkte angewendet werden. Thermoschneiden kann mit dem gleichen Verfahren und den gleichen Parametern wie für Schneiden von Baustahl durchgeführt werden, ausgenommen, dass für Gas- und Plasmaschneiden Maßnahmen getroffen werden müssen, um Wasserstoffrisse an der Kante und um sie herum zu vermeiden.
- Plasmaschneiden soll nur mit Sauerstoff als Plasmagas durchgeführt werden, um die Schneidkantenqualität zu optimieren. Wird ein Sekundärgas eingesetzt, gibt es für die chemische Zusammensetzung des Gases weniger Einschränkungen. Luft oder reiner Sauerstoff sind beide geeignet und sind die am meisten verwendeten Gase.
- Die nachträgliche Erwärmung der Schneidkante wird empfohlen, um eine optimierte maschinelle Bearbeitbarkeit einer Thermoschnittkante zu erreichen. Zusätzlich erhöht die nachträgliche Erwärmung den Widerstand gegen Wasserstoffrisse in der Schneidkante. Die nachträgliche Erwärmung ist für Gasschneiden vorzuziehen, aber für Plasma- oder Laserschneiden typischerweise nicht notwendig.
Die Hauptgründe für die Bildung von Wasserstoffrissen durch Thermoschneiden sind die gleichen wie für ihr Auftreten beim Schweißen. Dies bedeutet, dass die folgenden drei Bedingungen gleichzeitig vorhanden sein müssen, damit sich Wasserstoffrisse bilden können.
- Eine spröde Mikrostruktur der am geringsten betroffenen Zone (HAZ) des zu schneidenden Prüflings.
- Zu hohe Restbeanspruchungen in der Schneidkante und um sie herum.
- Vorhandensein von Wasserstoff im Stahl. Dieser Punkt ist in erster Linie ein Ergebnis der chemischen Zusammensetzung des Stahls. Jedoch lässt sich der Wasserstoffanteil in der HAZ, wo sich Wasserstoffrisse bilden können, durch verschiedene Maßnahmen reduzieren.
Die folgenden Maßnahmen werden empfohlen, um Wasserstoffrisse zu vermeiden und/oder die Bearbeitbarkeit einer Struktur zu optimieren, die Brennschneiden und Plasmaschneiden unterzogen wird. Die Maßnahmen werden in der Reihenfolge angegeben, in der sie auszuführen sind.
1. Vorwärmen in der Schneidkante und um sie herum, ausgeführt, um einen erhöhten Widerstand gegen Wasserstoffrisse zu erreichen, da es die Wasserstoffmigration von der HAZ zu den entsprechenden Teilen des Grundmetalls erleichtert.
2. Durchführen von Thermoschneiden.
3. Nachträgliche Erwärmung in der Schneidkante und um sie herum.
4. Abkühlung an Luft, wo Teile auf Umgebungstemperatur abgekühlt werden.
5. Bewertung des ausgeführten Schneidverfahrens.
Maßnahmen nach 1, 3 und 4 fördern einen höheren Widerstand gegen Wasserstoffrisse. Die Gründe dafür sind, dass all diese Maßnahmen die Wasserstoffmigration von der FAZ zum umgebenden Grundmatall fördern.
Maßnahmen die Wasserstoffmigration von der FAZ zum umgebenden Grundmatall fördern.
- It is not necessary in order to avoid
- The quality of the cut edge will decrease
Vorwärmung
Vorwärmung in der Schneidkante und um sie herum ist nur erforderlich, um Wasserstoffrisse zu vermeiden. Es kann nach verschiedenen Techniken durchgeführt werden. Die üblichsten Methoden sind der Einsatz einer der folgenden Techniken:
- Erwärmung in einem Ofen
- Einsatz von Vorwärmbrennern
- Benutzung von Elektromatten
Die minimale und maximale Vorwärm/Zwischenlagentemperaturen werden in der untenstehenden Tabelle angegeben.
Erwärmung in einem Ofen ist typischerweise das beste Verfahren, da es eine einheitliche Erwärmung des gesamten Teils fördert. Wenn Vorwärmbrenner benutzt werden, ist es wichtig, sie kontinuierlich in Bewegung zu halten, um die max. Vorwärmtemperatur des Toolox-Produkts nicht zu überschreiten.
The minimum holding time is set by the time it takes to get the opposite side to be heated to reach the required mini-mum preheat temperature. One example of a Die Mindesthaltezeit wird durch die Zeit festgelegt, die benötigt wird, um die gegenüberliegende Seite zu erwärmen, um die erforderliche min. Vorwärmtemperatur zu erreichen. Ein Beispiel für eine gute Praxis ist die Erwärmung über Nacht und dann das Schneiden am nächsten Morgen zu beginnen n. Sicherstellen, dass beide Seiten des Blechs keine Temperatur über den in der obigen Tabelle angegebenen max. Vorwärmtemperaturen erreichen..
Nachträgliche Erwärmung
Ähnlich wie die Vorwärmung erleichtert die nachträgliche Erwärmung eine weitere Wasserstoffmigration von der HAZ. Deswegen muss eine nachträgliche Erwärmung so schnell wie möglich nach dem Abschluss des Scheidens in einem maximalen Abstand von 60 Minuten zwischen dem Beginn des Schneidevorgangs und dem Beginn der nachträglichen Erwärmung g durchgeführt werden. Die nachträgliche Erwärmung ist vorzugsweise in einem Ofen durchzuführen, da es dies leichter macht, die Temperatur des Prüflings zu kontrollieren.
Die erhöhten Temperaturen entsprechen der untenstehenden Tabelle.
Die Aufsaugzeit soll 5 min/mm Dicke oder mindestens 60 min. betragen, gerechnet ab dem Zeitpunkt wo das Mittelteil die gewünschte Wärmebehandlungstemperatur erreicht hat. Normalerweise ist eine Aufsaugzeit von 2 Stunden ausreichend.
Bewertung des ausgeführten Schneidverfahrens
Kalibrieren Sie Ihr Verfahren zur nachträglichen Erwärmung durch die Härtekontrolle des Schweißguts und der von der Wärme betroffenen Zone. Das Schweißgut soll keine Härteverschlechterung aufweisen, Die von der Wärme betroffene Zone soll die gleiche oder fast die gleiche Härte wie das nicht betroffene Schweißgut haben.
FRÄSEN VON KANTEN NACH GASSCHNEIDEN
Um das Risiko von Wasserstoffrissen weiter zu verringern sowie Beanspruchungen zu entfernen, können die Gasschnittkanten durch Fräsen entfernt werden. In diesem Fall müssen 10 mm von der Schnittkante entfernt werden, um sicherzustellen, dass kein nicht betroffenes Material erreicht wird. Das Fräsen sollte so schnell wie möglich nach dem Thermoschneiden erfolgen.
ABRRASIVES WASSSERSTRAHLSCHNEIDEN
Abrasives Wasserstrahlschneiden (AWJ) ist ein alternatives Verfahren zum Thermoschneiden . Schneiden mit AWJ kann mit sehr guten Ergebnissen durchgeführt werden. Da AWJ während des Schneidens keine Wärme einbringt, ist das Risiko von Wasserstoffrissen sehr niedrig. AWJ von Toolox®-Produkten kann mit den gleichen Parametern wie für Schneiden von Baustahl erfolgen, und Vorwärmung und nachträgliche Erwärmung sind nicht erforderlich.
|
Vorwärmung |
Nachträgliche ErwärmungMax |
Stahl |
Min. Vorwärmung/
Zwischenlagentemperatur [°C] |
Max. Vorwärmung/
Zwischenlagentemperatur [°C] |
Temperaturintervall für
nachträgliche Erwärmung [°C] |
Toolox® 33 |
150 |
580 |
560 - 580 |
Toolox® 44 |
225 |
580 |
560 - 580 |