Vorwärm- und Zwischenlagentemperaturen für Hardox
Die für das Schweißen empfohlenen min. Vorwärm- und Zwischenlagentemperaturen werden in den Tabellen 5a, 5b und 6 angegeben. Sofern nicht etwas anderes angegeben ist, gelten diese Werte für Schweißen mit unlegierten und niedriglegierten Schweißzusatzwerkstoffen.
- Wenn Bleche unterschiedlicher Dicke aber aus der gleichen Stahlqualität zusammengeschweißt werden, bestimmt das dickere Blech die erforderlichen Vorwärm- und Zwischenlagentemperaturen; siehe Abbildung 4.
- Wenn verschiedene Stahlarten zusammengeschweißt werden, bestimmt das die höchste Vorwärmtemperatur verlangende Blech die erforderlichen Vorwärm- und Zwischenlagentemperaturen.
- Tabelle 5 gilt für einen Wärmeeintrag von 1.7 kJ/mm (43.2 kJ/Zoll) oder höher. Wenn ein Wärmeeintrag von 1.0 – 1.69 kJ/mm (25.4 – 42.9 kJ/Zoll) benutzt wird, empfehlen wir, dass Sie die Temperatur um 25°C (77°F) über die empfohlene Vorwärmtemperatur erhöhen.
- Wenn ein niedrigerer Wärmeeintrag als 1.0 kJ/mm (25.4 kJZoll) angewendet wird, empfehlen wir, dass Sie die SSABs WeldCalc-Software benutzen, um die empfohlene Mindestvorwärmtemperatur zu berechnen.
- Wenn die Umgebungsfeuchtigkeit hoch ist oder die Temperatur unter 5°C (41°F), sollte die in Tabelle 5a angegebene niedrigste empfohlene Vorwärmtemperatur um 25°C (77°F) erhöht werden.
- 4 Für Doppel-V-stumpfschweißnähte mit einer Dicke über 30 mm (1.181”) empfehlen wir, die Wurzellage um ca 5 mm (0.197”) von der Blechmittellinie entfernt zu legen.
Abbildung 5a:Empfohlene Vorwärmtemperaturen. Die einzelne Blechdicke in Millimetern wird in der x-Achse angegeben Empfohlener max. Wärmeeintrag für Hardox
Abbildung 5b: Empfohlene Vorwärmtemperaturen. Die einzelne Blechdicke in Zoll wird in der x-Achse angegeben.
Max- empfohlene Vorwärm- und Zwischenlagentemperaturen für unterschiedliche Einzelblechdick
Abbildung 4 Schematische Zeichnung für "Einzelblechdicke” 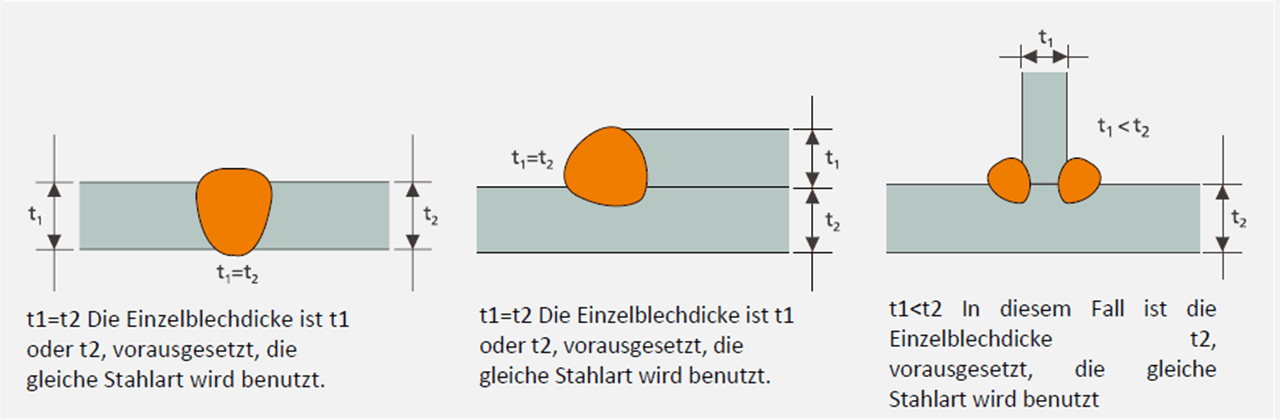
Die in Tabelle 6 angegebene Zwischenlagentemperatur ist die empfohlene max. Temperatur in der Schweißnaht (oben auf dem Schweißgut) oder unmittelbar angrenzend an die Schweißnaht (Startposition), gerade vor Beginn der nächsten Schweißlage.
Tabelle 6:Maximal empfohlene Zwischenlagen/Vorwärmtemperatur.
Hardox HiTemp |
300°C (572°F) |
Hardox HiTuf** |
300°C (572°F) |
Hardox 400 |
225°C (437°F) |
Hardox 450 |
225°C (437°F) |
Hardox 500 |
225°C (437°F) |
Hardox 550 |
225°C (437°F) |
Hardox 600 |
225°C (437°F) |
Hardox Extreme |
100°C (212°F) |
** Zwischenlagentemperaturen von
bis zu ca. . 400°C (752°F) können in
bestimmten Fällen für Hardox HiTuf
benutzt werden, konsultieren Sie in
solchen Fällen WeldCalc.
Die empfohlenen min. Vorwärmtemperaturen und max. Zwischenlagentemperaturen nach den Tabellen 5 und 6 sind nicht betroffen von Wärmeeinträgen höher als 1.7 kJ/mm (43.2 kJ/Zoll). Die Informationen basieren auf der Annahme, dass die Schweißnaht auf Umgebungstemperatur abgekühlt werden kann. Es wird darauf hingewiesen, dass diese Empfehlungen auch für Heftschweißungen und Wurzellagen gelten. Generell sollte jede Heftschweißung mindestens 50 mm (2”) lang sein. Für Schweißnähte an einer Blechstärke von bis zu . 8 mm (0.31”) können kürzere Heftschweißungen angewendet werden Der Abstand zwischen Heftschweißnähten kann entsprechend den Erfordernissen verändert werden.